Don't miss our holiday offer - 20% OFF!
In the industrial world, especially in the energy and transportation sectors, fuel quality is a crucial factor that affects efficiency, performance, and operational safety. Fuel quality sensors play an important role in ensuring that the fuel used meets the required standards. This article will discuss how fuel quality sensors work, the advanced technologies used, as well as the benefits and challenges of their implementation.
Contents
What Is a Fuel Quality Sensor?
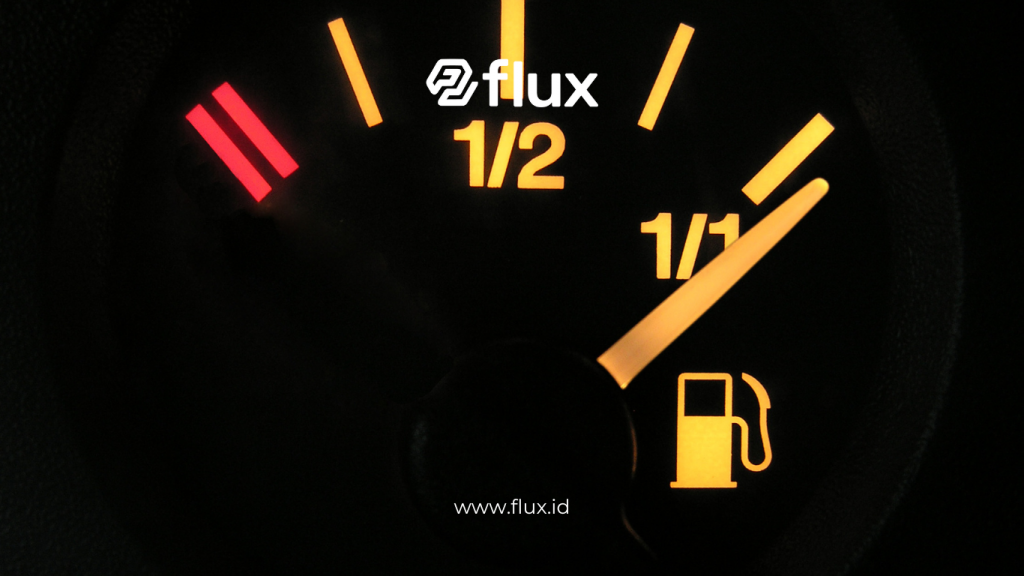
A fuel quality sensor is a device designed to monitor and analyze fuel quality in real-time. This sensor measures various fuel parameters such as density, viscosity, water content, and other contaminants to ensure that the fuel used meets established standards.
Primary Functions of Fuel Quality Sensors
- Monitoring Fuel Cleanliness: This sensor detects the presence of contaminants or dirt in the fuel, which can affect engine performance and energy efficiency.
- Measuring Density: Fuel density is an important indicator for determining the quality and consistency of the fuel.
- Controlling Water Content: Water content in the fuel can cause corrosion and damage to the engine. The sensor helps ensure that water levels remain within safe limits.
- Assessing Viscosity: Fuel viscosity affects flow and combustion. The sensor monitors viscosity to ensure efficient fuel burning.
Advanced Technologies in Fuel Quality Sensors
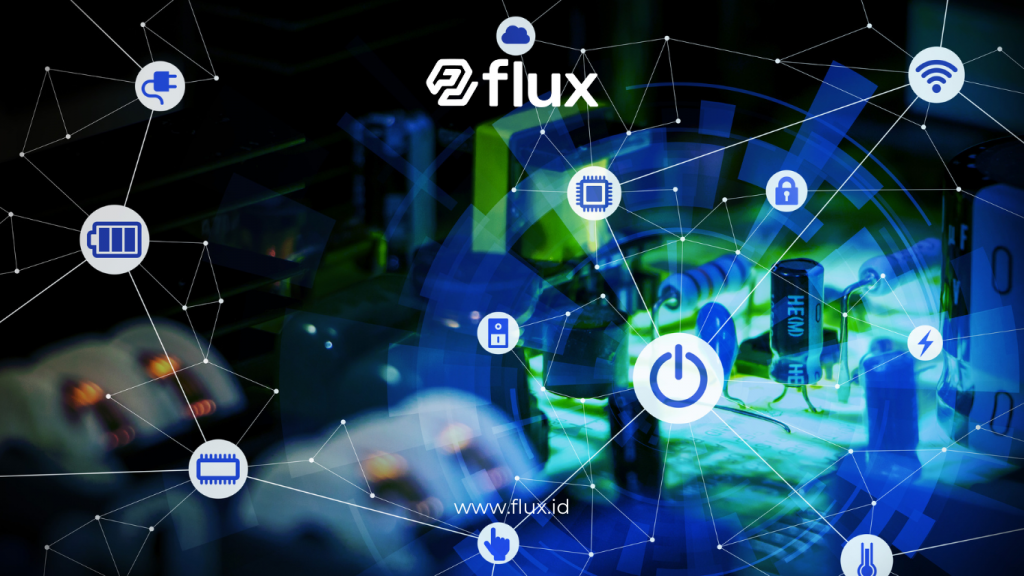
Read More : Advanced Fuel Quality Sensors in Tank Monitoring
Fuel quality sensors use various advanced technologies to provide accurate and reliable data. Here are some key technologies used:
Optical Technology
Optical sensors use light to analyze the fuel. By utilizing phenomena such as light scattering and absorption, these sensors can determine the presence and concentration of contaminants in the fuel. This technology offers high resolution and can detect contaminants at very low concentrations.
Electromagnetic Technology
Electromagnetic sensors measure changes in the electromagnetic properties of the fuel. This technology is often used to measure fuel density and viscosity. These sensors can provide real-time data with high accuracy, even in extreme operational conditions.
Capacitive Technology
Capacitive sensors measure changes in electrical capacitance caused by the fuel. These changes in capacitance can be used to determine water content and the presence of contaminants. Capacitive sensors are useful in applications where the fuel has variations in composition and conditions.
Ultrasonic Technology
Ultrasonic sensors use high-frequency sound waves to analyze the fuel. This technology can be used to measure viscosity and density of the fuel. Ultrasonic sensors provide rapid results and can be used for real-time monitoring.
How Fuel Quality Sensors Work
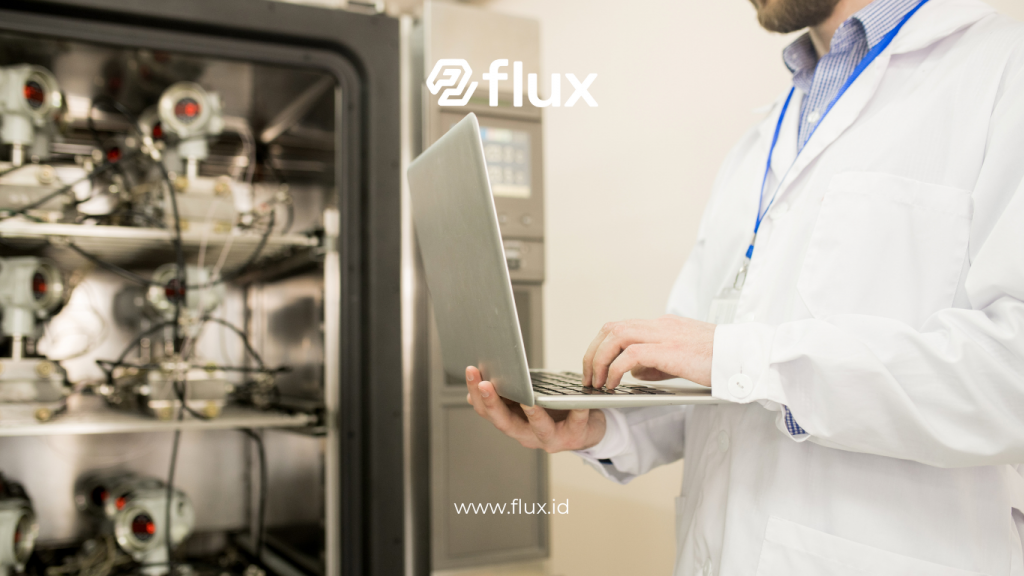
Read More : How Fire and Gas Sensors Work: Ensuring Smart City Safety with Advanced Technology
Installation of Sensors in Tanks
Fuel quality sensors are typically installed inside or around the fuel tank. The installation process involves placing the sensor in strategic positions to ensure effective monitoring. These sensors are connected to control systems to transmit the collected data.
Data Collection
Once installed, the sensors begin to collect data continuously. The collected data includes parameters such as density, viscosity, and water content. The sensors send this information to the connected control systems, which then process and analyze the data.
Analysis and Interpretation
The control systems analyze the data collected by the sensors to determine fuel quality. If deviations from the established standards are detected, the system can send alerts or activate corrective actions, such as separating fuel that does not meet standards.
Corrective Actions
Based on the data analysis, corrective actions can be taken to address fuel quality issues. This may include cleaning the tank, separating contaminants, or adding additives to improve fuel quality.
Benefits of Fuel Quality Sensors
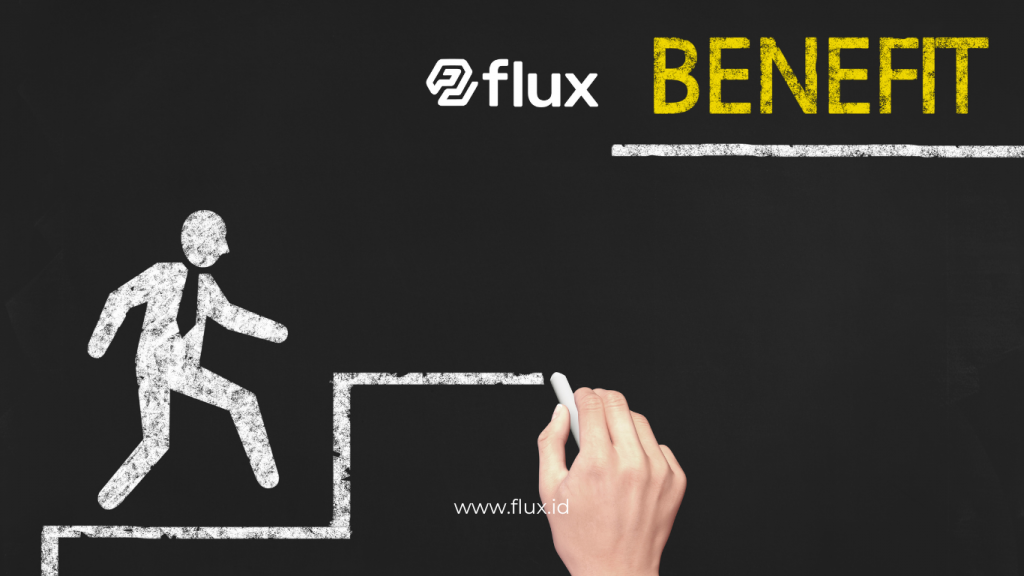
Read More : Enhancing Motor Health: Dust Sensor’s Role for Better Air Quality
Improving Operational Efficiency
By monitoring fuel quality in real-time, sensors help ensure that the fuel used is of the highest quality, thereby improving operational efficiency and engine performance.
Reducing Engine Damage Risks
Contaminants and poor fuel quality can cause engine damage. By detecting issues early, sensors help reduce the risk of damage and repair costs.
Ensuring Compliance with Standards
Fuel quality sensors help ensure that the fuel meets established standards, both in terms of efficiency and safety. This is important for complying with industry regulations and avoiding potential legal issues.
Enhancing Safety
By monitoring water content and contaminants, sensors help prevent issues that could lead to engine failure or safety incidents. This is crucial in industrial and transportation applications that require high safety standards.
Challenges in Implementing Fuel Quality Sensors
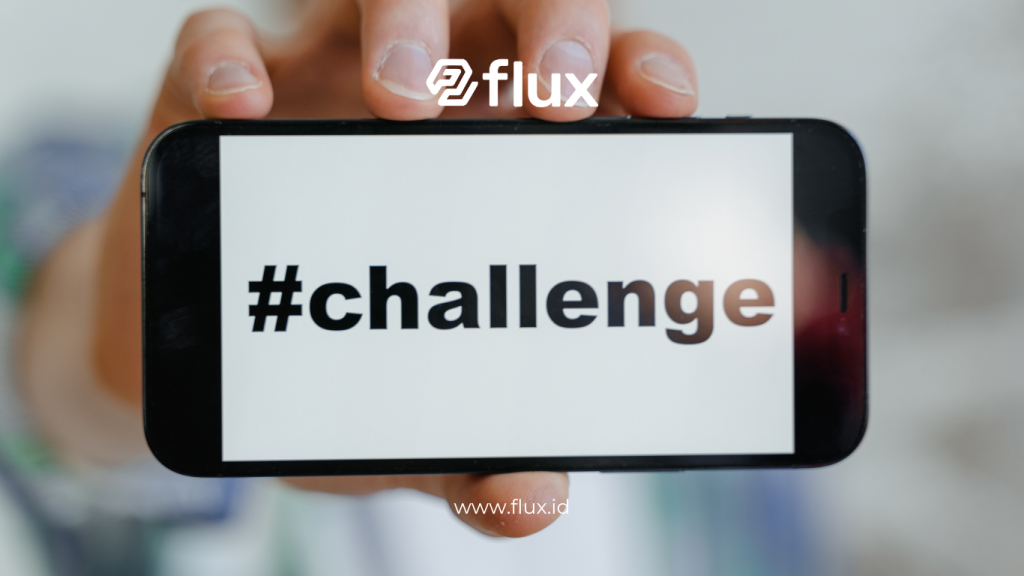
Read More : Overcoming Farmer Challenges with IoT Solutions
Initial Cost
One of the main challenges in implementing fuel quality sensors is the initial cost. Advanced sensor devices can be quite expensive, which might be a burden for some companies.
Maintenance and Calibration
Fuel quality sensors require routine maintenance and calibration to ensure data accuracy. This process can be time-consuming and resource-intensive, requiring technical expertise.
Operational Environment
Sensors must operate effectively under various conditions, including extreme temperatures and chemical exposure. Choosing sensors that can handle harsh operational environments is crucial for long-term performance.
System Integration
Integrating sensors with existing control systems can be challenging, especially if the systems are not designed to receive data from fuel quality sensors. Efforts are needed to ensure that sensor data can be effectively utilized within existing systems.
Conclusion
Fuel quality sensors are advanced technologies that play a vital role in ensuring fuel quality in tanks. By using technologies such as optical, electromagnetic, capacitive, and ultrasonic, these sensors can monitor various fuel parameters and ensure that the fuel used meets established standards.
The main benefits of fuel quality sensors include improved operational efficiency, reduced engine damage risks, compliance with standards, and enhanced safety. Although there are challenges such as initial cost, maintenance, and system integration, the benefits often outweigh these challenges.
With the continued advancement of technology, fuel quality sensors will become increasingly sophisticated and efficient, helping industries better manage and maintain fuel quality. The implementation of these sensors will play a crucial role in ensuring that the fuel used in various applications is of the highest quality, supporting operational efficiency and safety.
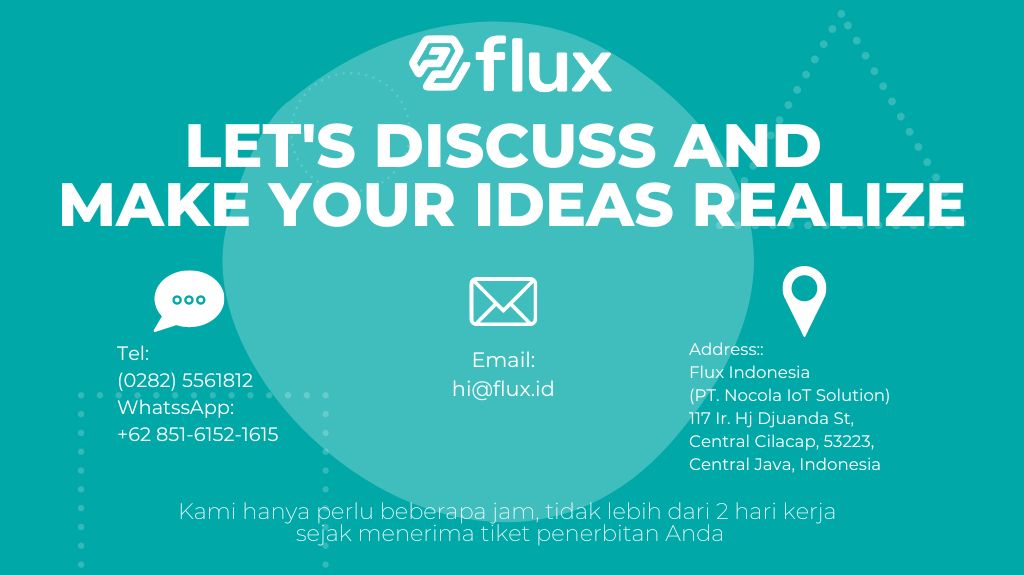
4o mini