Don't miss our holiday offer - 20% OFF!
In an increasingly complex and competitive industrial world, operational efficiency is crucial for success. One approach that has been gaining popularity is the use of Internet of Things (IoT) technology for machine health monitoring. IoT sensors provide real-time data on machine conditions, enabling companies to perform predictive maintenance, which not only reduces downtime but also improves efficiency and extends the lifespan of machines. This article will explore the role of IoT sensors in machine health monitoring, the benefits they offer to the manufacturing industry, and effective strategies for implementation.
Contents
- 1 1. What is an IoT Sensor?
- 2 2. The Importance of Machine Health Monitoring
- 3 3. How IoT Sensors Enhance Predictive Maintenance
- 4 4. Implementing IoT Sensors in Predictive Maintenance
- 5 5. Challenges in Implementing IoT Sensors
- 6 6. Case Study: IoT Sensor Implementation in Manufacturing
- 7 7. The Future of IoT Sensors in Predictive Maintenance
- 8 Conclusion
1. What is an IoT Sensor?

An IoT sensor is a device connected to the internet that can collect and transmit data. In the manufacturing industry, these sensors are widely used to monitor various machine parameters such as temperature, vibration, pressure, and humidity. With IoT technology, the data collected can be analyzed in real-time, providing deep insights into machine performance.
1.1 Types of IoT Sensors
Several types of IoT sensors are commonly used in the manufacturing industry:
- Temperature Sensors: These monitor machine temperatures to prevent overheating.
- Vibration Sensors: They detect abnormal vibrations, which may indicate damage.
- Pressure Sensors: These ensure that the system pressure stays at safe levels.
- Humidity Sensors: These monitor humidity levels, which can affect machine performance.
2. The Importance of Machine Health Monitoring
Monitoring the health of machines is vital in the manufacturing industry for several reasons. First, it reduces downtime by identifying issues before they escalate, thus preventing unexpected production halts. Additionally, it extends the lifespan of machines by keeping them in optimal condition. Furthermore, predictive maintenance saves costs by allowing companies to only perform maintenance when necessary, instead of following a rigid schedule. Finally, machines that function optimally contribute to more efficient production processes, which, in turn, improves overall productivity.
3. How IoT Sensors Enhance Predictive Maintenance

Read More: Improving Air Quality with IoT Sensors: Pollution Monitoring Solutions for a Healthy Environment
Predictive maintenance relies on data to forecast when maintenance will be needed. IoT sensors play a crucial role in this process by continuously collecting real-time data about machine conditions, which companies can analyze quickly and accurately. By using machine learning algorithms and big data analytics, companies can study both historical and real-time data to identify patterns and predict potential failures. Moreover, the system can send notifications and alerts to the maintenance team when the sensors detect unusual conditions, allowing them to take immediate action before the problem worsens.
4. Implementing IoT Sensors in Predictive Maintenance
To successfully implement IoT sensors in predictive maintenance, companies must follow several key steps.
4.1 Needs Assessment
First and foremost, companies should assess their specific needs regarding machines and production processes. Identifying critical parameters that require monitoring is essential to ensure the system is tailored to the company’s needs.
4.2 Selecting the Right Sensors
Once the needs have been identified, companies should carefully select sensors that are suitable for their operating environment and machine type. For instance, machines that operate in extreme conditions may require heat-resistant or moisture-resistant sensors.
4.3 Integration with Existing Systems
In addition to selecting the right sensors, it is essential to integrate the IoT sensors with existing maintenance management systems, such as Enterprise Resource Planning (ERP) or Computerized Maintenance Management Systems (CMMS). This integration ensures that sensor data can be effectively utilized in decision-making processes.
4.4 Training and Skills Development
Another key aspect of implementation is ensuring that the maintenance team is well-trained in using the sensors and analyzing the data. Having staff who are proficient in data analysis will significantly enhance decision-making and overall maintenance effectiveness.
5. Challenges in Implementing IoT Sensors
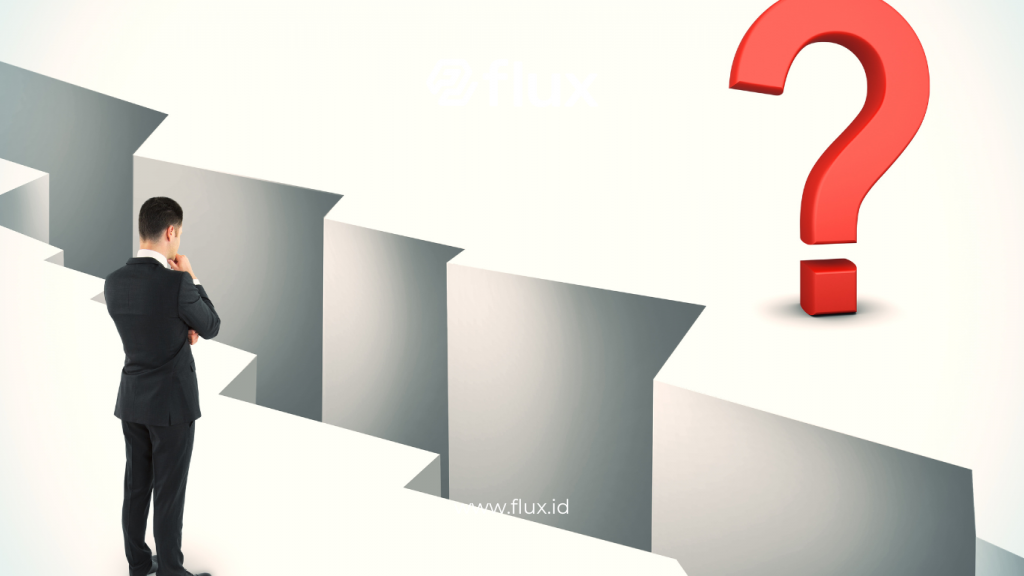
Read More: IoT Sensors in Asset Management: Opportunities and Challenges
While IoT sensors provide numerous benefits, their implementation is not without challenges.
5.1 Data Security
First, data security is a major concern, as IoT devices are often connected to a network. Companies must implement stringent security measures to protect sensitive data from unauthorized access or cyberattacks.
5.2 Initial Costs
Second, the initial investment in hardware, software, and training can be high. However, companies should consider the potential long-term cost savings from reduced downtime and more efficient maintenance practices.
5.3 Compatibility
Lastly, some machines may not be designed to support IoT sensors, which can pose a barrier to implementation. In these cases, companies may need to invest in equipment upgrades to fully benefit from IoT technology.
6. Case Study: IoT Sensor Implementation in Manufacturing
For example, an automotive manufacturing company decided to implement IoT sensors to monitor the health of its assembly line machines. By installing temperature and vibration sensors, the company was able to reduce machine downtime by 30% within the first year. This success demonstrates the potential of IoT sensors in improving operational efficiency and reducing production costs.
7. The Future of IoT Sensors in Predictive Maintenance
Looking ahead, the future of IoT sensors in predictive maintenance is very promising. With advances in 5G technology and artificial intelligence, IoT sensors will be able to provide even more accurate and faster analysis. As a result, companies that invest in IoT technology will gain a significant competitive edge in the manufacturing industry.
Conclusion
In conclusion, IoT sensors for machine health monitoring offer a highly effective solution for predictive maintenance in the manufacturing industry. By collecting and analyzing real-time data, these sensors help companies reduce downtime, extend machine lifespan, and lower maintenance costs. Although challenges exist, the long-term benefits far outweigh them. As IoT technology continues to evolve, companies that adopt these solutions will have a substantial advantage in the rapidly advancing world of smart manufacturing.
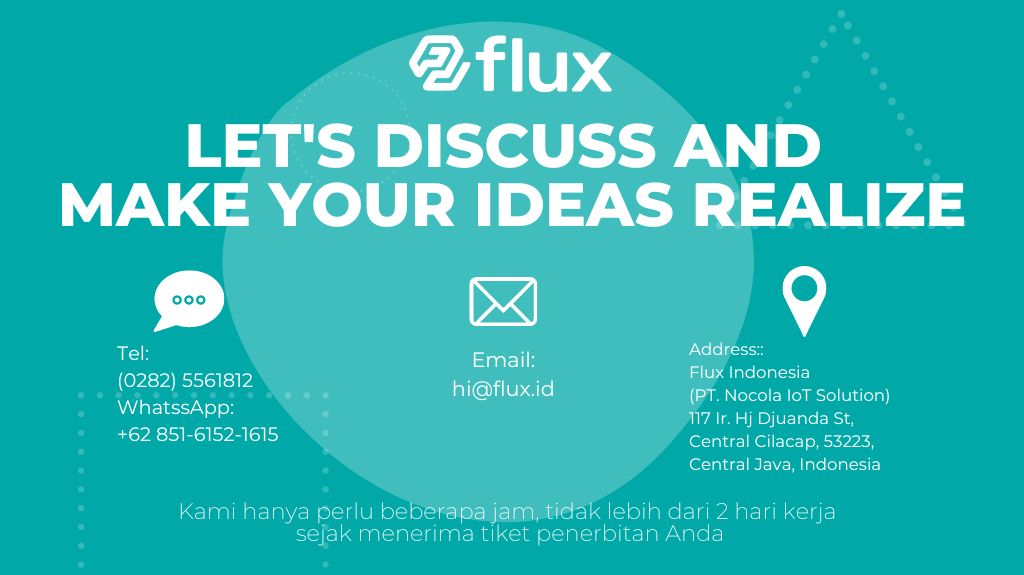